Approfondimenti
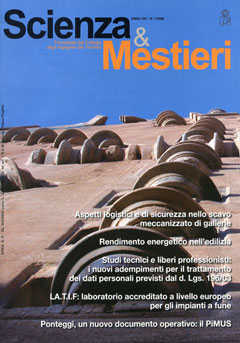
di Roberto Gazzi
Il progetto per il raddoppio della S.S. 47 della Valsugana nel tratto Ponte Alto - Trento Nord - Variante di Martignano, realizzato dalla Provincia Autonoma di Trento, ha previsto lo scavo di due gallerie naturali di circa 2750 metri sotto gli abitati di Martignano e Cognola. Per ridurre il disturbo arrecato dai lavori ad un’area così densamente popolata fu imposto già in sede progettuale l’uso di una fresa meccanica a piena sezione per lo scavo di gallerie, o TBM (Tunnel Boring Machine). L’impresa TOTO Costruzioni S.p.A. di Chieti, capogruppo dell’A.T.I. alla quale furono affidati i lavori, fece quindi realizzare alla ditta HERRENKNECHT AG di Schwanau (D), azienda leader del settore, la TBM S-251 Valsugana Trento Nord, una fresa scudata per roccia dura del diametro di 12,11 metri.
Dal 26 settembre 2003, giorno di arrivo dei primi pezzi al cantiere di Martignano, al 25 gennaio 2006, giorno in cui la testa è uscita all’esterno per la seconda volta, si è esaurito il lavoro di “Tecla” (così è stata subito ribattezzata la TBM dalle maestranze impegnate nell’opera) ed ora ci si appresta allo smontaggio finale.
Oltre ad alcune sommarie informazioni tecniche sulle caratteristiche e sulla metodologia di scavo della macchina, sulla scorta dei dati raccolti durante i lavori si vogliono qui presentare alcuni aspetti operativi relativi all’uso della fresa.
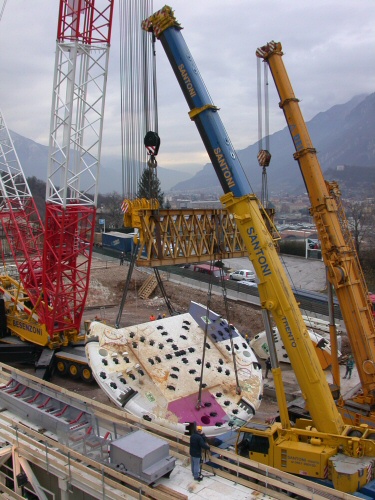
La TBM è composta da due parti distinte:
- il sistema meccanizzato scudo-testa fresante (lungo circa 10 m), che scava sostenendo il fronte e che mette in opera il rivestimento;
- il back-up (lungo circa 150 m) composto da un sistema di carri agganciati alla testa, che trasporta tutti gli impianti di servizio.
All’interno della sezione anteriore dello scudo si trova il cuscinetto, che imprime la rotazione alla testa, e l’erettore dei conci, un braccio meccanico dotato di un sistema vacuum che permette il sollevamento ed il posizionamento dei conci. Completa la parte anteriore della TBM la coda dello scudo, un anello di acciaio dello spessore di 50 mm saldato in opera alla parte anteriore.
Il back-up è composto da cinque carri mobili su rotaie, con i servizi e gli impianti principali, e da una piattaforma inferiore su ruote gommate, che costituisce la zona di arrivo dei mezzi per i rifornimenti. La slitta per il rifornimento dei conci all’erettore, agganciata direttamente alla testa, completa il sistema di supporto.
Il primo carro è quello dove sono concentrati gli elementi più importanti e indispensabili al funzionamento della macchina: la cabina di regia, dove si trovano i comandi ed i monitor di controllo di avanzamento e posizione della testa; i motori oleodinamici e l’impianto di trasformazione e distribuzione dell’energia elettrica; il filtro dell’aria aspirata dalla tramoggia di scarico del marino. L’alimentazione della TBM avviene direttamente con una linea dedicata da 20.000 V, per una potenza massima installata di 5 MVA.
Sul secondo carro trovano posto i generatori di aria compressa, gli impianti per l’iniezione di pea-gravel (il ghiaino a diametro controllato utilizzato per saturare i vuoti tra anelli prefabbricati ed ammasso roccioso) e la piattaforma inferiore di carico dei conci.
Gli altri tre carri, che sovrastano la piattaforma inferiore, ospitano le riserve di cavi (alimentazione, impianto di terra, telefono, trasmissione dati) e tubazioni (andata e ritorno liquido del circuito di raffreddamento) per l’avanzamento ed una vasca di decantazione.
Per l’approvvigionamento dei conci alla slitta vengono impiegati due carriponte: uno sulla parte superiore del back-up, che preleva i conci dagli autocarri e li deposita sulla piattaforma inferiore del secondo carro; uno nella parte inferiore dei primi due carri, che completa il trasferimento dei prefabbricati alla slitta.
L’intero back-up è attraversato dal nastro trasportatore: una prima sezione preleva il marino dalla tramoggia di scarico della testa e lo deposita sulla seconda sezione che arriva all’ultimo carro; da qui parte la sezione di nastro che arriva fino all’esterno, sostenuta da supporti fissati direttamente alla volta della galleria.
La piattaforma inferiore è dotata di una pedana girevole sulla quale gli automezzi possono invertire il senso di marcia ed evitare così lunghe e pericolose retromarce in galleria.
Complessivamente la macchina, lunga circa 160 metri e del peso di circa 2000 tonnellate (di cui metà nella sola parte anteriore) è composta da oltre 3 milioni di pezzi. Per trasportarli al cantiere di Martignano si sono resi necessari una sessantina di trasporti, di cui 19 eccezionali. Tra questi, il trasporto più delicato è stato quello del cuscinetto, pezzo di 6 m di diametro con un peso di 180 t.
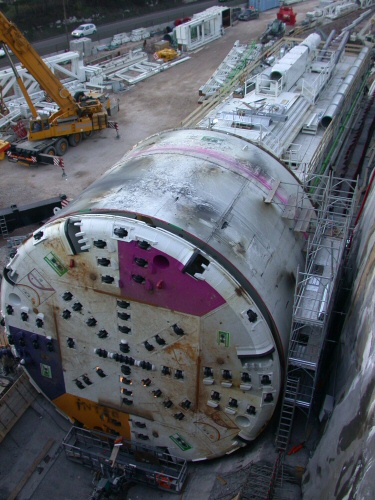
Per potere assemblare una TBM ed avviare lo scavo è necessario realizzare alcune opere preliminari. Sul fronte di attacco si scava con tecniche tradizionali un primo tratto di galleria a sezione circolare, lungo una decina di metri. Dietro l’imbocco viene realizzato l’arco rovescio della galleria artificiale esterna, formato dalla culla, dove avviene il montaggio della testa, e dalla rampa di lancio, dove viene assemblato il back-up.
Ultimato lo scudo della TBM si provvede a montare la struttura di contrasto, contro la quale viene montato il primo anello di conci prefabbricati. Quando la testa è in grado di muoversi, viene realizzato il tratto di attacco, costituito da anelli di conci a cielo aperto mantenuti in posizione da funi di acciaio ancorate alle murette, che verrà successivamente inglobato nel getto del primo tratto di galleria artificiale. Solo a questo punto la TBM può avanzare fino al fronte, mettendo in opera gli anelli nel tratto di galleria naturale, e quindi iniziare l’effettivo scavo. All’altro imbocco si scava con tecniche tradizionali l’ultimo tratto di galleria a sezione circolare e, all’esterno, si costruisce la culla per lo smontaggio della TBM.
Nelle prime fasi di scavo lo smarino avviene con autocarri che raccolgono il materiale da una tramoggia posta al termine del secondo nastro trasportatore. Solo quando la TBM è completamente dentro il tunnel è possibile montare il nastro esterno e la ventilazione ed incominciare così lo scavo a pieno regime.
Dal punto di vista operativo lo scavo con TBM avviene in due fasi distinte, che in questo tipo di macchina (monoscudata) sono necessariamente sfalsate temporalmente: la fase di scavo e la fase di montaggio dell’anello di rivestimento.
Durante la fase di scavo la testa ruota e preme contro il fronte con una forza di spinta che può raggiungere 7000 t. Sia la velocità di rotazione che la forza di spinta vengono controllate dalla cabina di regia, per variare la velocità di avanzamento nell’ammasso roccioso anche in funzione del tipo di roccia scavata. I cutters, che girano su se stessi per effetto del movimento della testa, incidono la roccia con specifiche traiettorie e fanno saltare la roccia per effetto di trazione. La spinta della testa ed il conseguente avanzamento della TBM viene ottenuto per mezzo di 19 coppie di pistoni che si appoggiano sull’ultimo anello messo in opera. La lunghezza dello scavo di ogni fase è di 150 cm (la larghezza media dei conci) ed è interamente protetta dalla coda dello scudo, entro la quale sarà posto in opera l’anello.
Al termine della fase di scavo la TBM si arresta ed incomincia la fase di montaggio dell’anello.
Un anello è costituito da 7 conci in calcestruzzo armato normale, dello spessore di 40 cm: 6 conci lunghi circa 5,70 m, del peso di 8,6 t l’uno; 1 concio chiave, lungo circa 2,0 m. La larghezza media è di 150 cm e varia in funzione della tipologia di concio (conci universali). Secondo il posizionamento dell’anello, controllato dal computer di bordo, è possibile variare la direzione di avanzamento del tunnel. Per mettere in opera un concio vengono arretrati i pistoni alla posizione prestabilita dal computer. L’erettore preleva il pezzo dalla slitta con un sistema vacuum a tre ventose (una sola ventosa è sufficiente a sopportare il peso di un concio, per evitare la perdita del carico in caso di avaria) e lo posiziona nella sua sede. Si procede in successione fino all’ultimo concio (quello di chiave), il quale mette in compressione l’anello. I conci di un anello vengono imbullonati tra loro, in senso radiale, e sono collegati all’anello precedente mediante connettori o bulloni.
A ridosso del fronte si svolgono altre importanti operazioni per il completamento del rivestimento: l’iniezione con pea-gravel dei vuoti tra anello ed ammasso roccioso e l’iniezione con malta alla base dell’anello. La saturazione della parte iniettata col ghiaino viene effettuata con boiacca a scavo concluso, per permettere la redistribuzione delle tensioni nell’ammasso senza caricare la struttura di rivestimento.
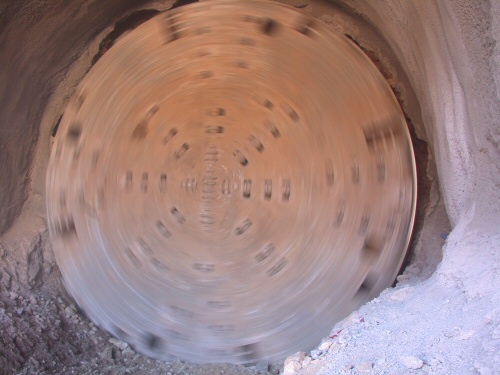
Il 26 settembre 2003, con l’arrivo dei pezzi della coda dello scudo, incomincia il primo montaggio della TBM S-251 e ci vorranno circa tre mesi per completare la macchina fino al punto da permetterle l’inizio dello scavo. La testa viene montata in una culla di calcestruzzo armato appositamente predisposta, che costituisce l’arco rovescio del tratto di attacco. Per poter reggere la spinta della macchina, che mette in opera già il 30 dicembre il primo concio e, a seguire, gli anelli del tratto di attacco, viene realizzata in cantiere una struttura di contrasto di acciaio, impuntata contro il primo anello. I primi anelli vengono ancorati alle murette con funi di acciaio e successivamente inglobati nella prima parte di galleria artificiale. Finalmente il 31 gennaio 2004 viene dato il primo giro ufficiale alla testa, nel corso della cerimonia di inaugurazione. Sono stati necessari 99 giorni di lavoro effettivo, di cui 24 per portare la TBM al punto di attacco.
Alla fine dello scavo della prima canna la TBM viene riportata agli imbocchi a valle. La testa viene smontata e trasportata al punto di partenza in 32 giorni (dal 7 febbraio al 15 marzo 2005, con trasporti eccezionali che hanno comportato la chiusura della S.S. 47 per alcune notti). Altri 18 giorni (dall’11 aprile al 2 maggio 2005) sono utilizzati per calare il back-up a ritroso lungo la galleria appena ultimata.
Nel secondo montaggio i tempi vengono dimezzati, dal momento che i pezzi sono tutti disponibili in cantiere ed in gran parte preassemblati. Viene scelta anche una nuova struttura di contrasto di acciaio, calcolata e realizzata per la spinta effettiva della macchina, che contribuirà a ridurre i tempi di attacco e di scavo della parte iniziale della galleria. 47 giorni lavorativi (dal 4 aprile al 28 maggio 2005), di cui 6 utilizzati per traslare il back-up dalla prima alla seconda rampa di lancio, sono sufficienti per completare questa fase.
Per le operazioni di montaggio si sono rese necessarie una gru Terex Demag TC 2800 7000 (braccio mobile da 21 m x 600 t in punta) ed una gru da 200 t. Un’ulteriore gru da 200 t è servita durante le operazioni di sollevamento della testa. Il personale impiegato nelle suddette operazioni è stato di circa 50 unità, con turni di lavoro sufficienti a coprire 24 ore su 24, per 6 giorni la settimana.
Il tiro più rilevante è stato quello relativo alla traslazione dell’intero primo carro del back-up dalla prima alla seconda rampa di lancio, per un carico totale di circa 400 t; quello logisticamente più impegnativo è stato il sollevamento della testa preassemblata, per circa 200 t di carico, in cui sono state impegnate le tre gru contemporaneamente.
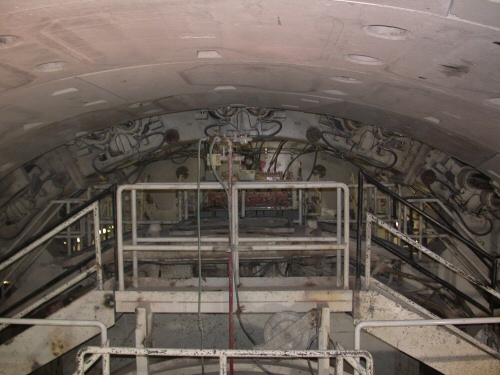
La media di scavo effettiva, sui circa 2720 metri di distanza tra i fronti delle gallerie di attacco, è stata di 9,8 metri/giorno, mentre quella totale compresa di attacco ed uscita è stata di 9,2 metri/giorno.
La TBM è in grado di ricominciare il lavoro per la realizzazione della canna di valle il 30 maggio 2005. In soli 6 giorni si esaurisce la fase di attacco e lo scavo effettivo si svolgerà dal 6 giugno al 12 dicembre, giorno dell’abbattimento dell’ultimo diaframma della canna di valle, all’interno del tratto scavato per circa 70 metri con tecniche tradizionali. Ai 156 giorni necessari per lo scavo effettivo, si aggiungeranno i 24 necessari per portare la macchina all’esterno (dal 13 dicembre 2005 al 25 gennaio 2006), per un totale di 186 giorni.
La media di scavo effettiva, sui circa 2670 metri di distanza tra i fronti delle gallerie di attacco, è stata di 17,1 metri/giorno, mentre quella totale compresa di attacco ed uscita è stata di 14,8 metri/giorno. La produzione di punta giornaliera si è registrata nello scavo della canna di valle, con 36 metri (24 anelli) di galleria scavata e rivestita. Il personale impiegato nelle operazioni di scavo è stato di circa 75 unità, con turni di lavoro sufficienti a coprire 24 ore su 24, per 6 giorni la settimana.
La media generale sullo scavo delle due gallerie è stata di 11,3 metri/giorno. Altri valori, di carattere più generale, si possono ottenere comprendendo nei tempi di produzione anche quelli di montaggio. Si possono così aggiungere i 98 giorni lavorativi intercorsi tra la fine della prima canna e l’inizio della seconda, per valutare la media complessiva compresa di fermo macchina, che scende a 9,4 metri/giorno, valore pur sempre superiore alla media totale della sola prima canna. Aggiungendo poi i 99 giorni necessari per il primo assemblaggio della TBM, otteniamo la media onnicomprensiva dall’inizio delle operazioni, che si attesta sugli 8,1 metri/giorno.
Il volume (in mucchio) del materiale di risulta originato dallo scavo delle due gallerie è stato di circa 900.000 metri cubi.
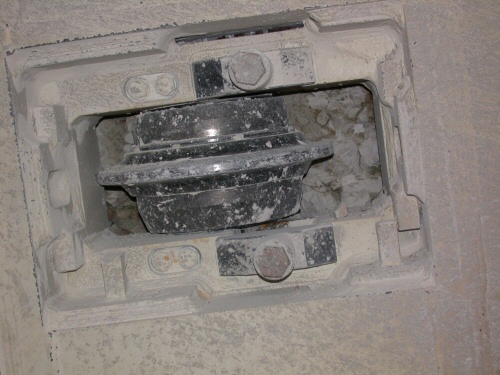
Le principali differenze operative tra la prima e la seconda canna sono state una diversa struttura di contrasto della spinta per l’avviamento della TBM, l’uso di centratori per i conci (connettori assiali in acciaio tipo biblock da inserire nel concio da porre in opera, che facilitano il corretto posizionamento del concio nella sua sede, realizzando al contempo la necessaria connessione longitudinale ed a taglio) e un diverso approccio per la preparazione degli imbocchi a Ponte Alto per l’uscita della TBM.
Si era già accennato sulle strutture di contrasto utilizzate: una struttura di contrasto di acciaio impuntata contro il primo anello, realizzata in cantiere a basso costo, per la prima canna; una specifica struttura di contrasto di acciaio, calcolata per la spinta effettiva della macchina e realizzata in un’officina di carpenteria metallica, per la seconda canna. Mentre per la seconda canna lo scavo è cominciato a ritmi normali, con significativa incidenza sui tempi complessivi, la prima canna ha avuto un rendimento iniziale estremamente basso, poiché la struttura allestita non si è rivelata in grado di sopportare la piena spinta della testa.
Sempre in un’ottica di contenimento dei costi, nella prima canna i connettori previsti in sede progettuale sono stati sostituiti con dei più economici bulloni da fissare a concio posizionato. Si è riscontrato che ciò a portato a sensibili allungamenti nei tempi di posa dell’anello, peggiorando anche la qualità estetica del rivestimento, la cui posa è risultata meno precisa. L’uso del centratore ha inoltre introdotto maggiore sicurezza nella fase lavorativa interessata, eliminando la presenza di persone a contatto del concio in posizionamento, che prima erano necessarie per ottenere l’allineamento dei fori per i bulloni.
L’analisi geologica del tratto finale (circa 150 metri) del tracciato delle gallerie evidenziò la presenza di terreno sciolto, poco adatto per lo scavo con TBM, e pertanto i progettisti ravvisarono la necessità di scavare con tecniche tradizionali gli imbocchi Est fino al limite della roccia. L’impresa optò per il consolidamento del terreno con la tecnica del jet-grouting, da scavare poi con la TBM.
Per la prima canna si sono registrati risultati inferiori alle aspettative nelle caratteristiche del terreno consolidato e ciò ha portato ad ulteriori rallentamenti nella produzione della fresa. Per la seconda canna si è adottata una soluzione di compromesso e, oltre a modificare i parametri per l’esecuzione del jet-grouting, si è allungato a circa 70 metri il tratto scavato in naturale, evitando in definitiva i ritardi nei tempi di scavo nella parte finale.
Le scelte operate dalla direzione di cantiere per la realizzazione della seconda canna (diversa da quella presente all’epoca di realizzazione della prima canna), inizialmente più onerose, si sono rivelate invece determinanti per ottimizzare il processo di produzione della seconda canna, riportando le medie complessive a valori discreti.
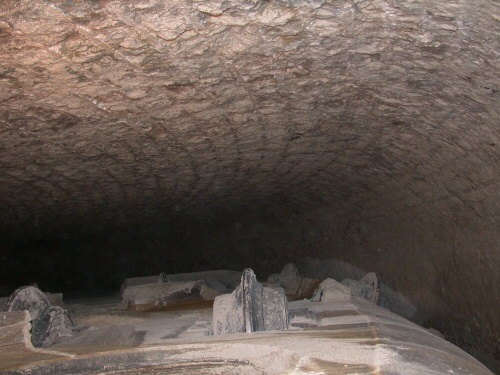
La soluzione dello scavo meccanizzato permette tempi di esecuzione più rapidi rispetto alla tecnica tradizionale ed è economicamente competitiva per le lunghezze qui affrontate. L’aspetto dei tempi di realizzazione non era secondario per un’opera di primaria importanza come la Variante di Martignano e per ottenere prestazioni superiori con un approccio tradizionale si sarebbe dovuto considerare lo scavo da quattro fronti, con grave disturbo alla popolazione ed inevitabile peggioramento delle condizioni di sicurezza in cantiere. Da qui, come detto in premessa, la scelta di imporre già in sede progettuale l’uso di una TBM, ottimizzando una serie di aspetti importanti per l’Amministrazione provinciale: i tempi di esecuzione, l’impatto sulla popolazione e la sicurezza nel lavoro.
Verranno ora esaminate le problematiche relative alla sicurezza e alla salute in cantiere, considerando in particolare l’incidenza statistica degli effettivi casi di infortunio.
Le fasi di montaggio e smontaggio della TBM sono tra quelle più delicate dell’intero processo di costruzione delle gallerie. I rischi presenti sono quelli relativi alla movimentazione di carichi pesanti (anche con uso contemporaneo di due o tre gru) ed alla caduta dall’alto, oltre a quelli relativi alle normali lavorazioni di cantiere. Le operazioni di sollevamento non hanno creato problemi di sicurezza, sia per la preparazione specifica degli operatori interessati che per l’attenzione posta nei tiri più problematici. Le operazioni di sollevamento sono state coordinate dall’operatore specializzato della ditta Delta Besenzoni S.p.A. (gru Terex Demag TC 2800 7000 da 600 t in punta), in particolare quando si è reso necessario l’uso di altre gru (da 200 t) in contemporanea. Non ci sono stati incidenti per caduta dall’alto, anche se è stato necessario un costante lavoro di repressione dei comportamenti scorretti dei lavoratori impegnati nelle operazioni, che tendevano a non usare i DPI anticaduta dove richiesto dalle procedure. Qualche problema si è invece avuto nelle operazioni di contorno, quali pulizia o smontaggio di parti di macchina. Complessivamente in queste fasi si sono verificati 8 infortuni non gravi, per totali 190 giorni di assenza per inabilità temporanea con una media di 23,75 giorni/infortunio. Le tipologie più rilevanti sono state la distorsione di un dito (durante l’uso di pistola pneumatica per bulloni e per scivolata accidentale) o tibio-tarsica (scivolata accidentale) e le contusioni (scivolate accidentali e caduta del carico trasportato dalle mani). Per i casi evidenziati non si rileva una mancanza di formazione ed informazione dei lavoratori o una carenza nelle procedure di sicurezza, quanto una predominanza del fattore umano (disattenzione o non elevata professionalità).
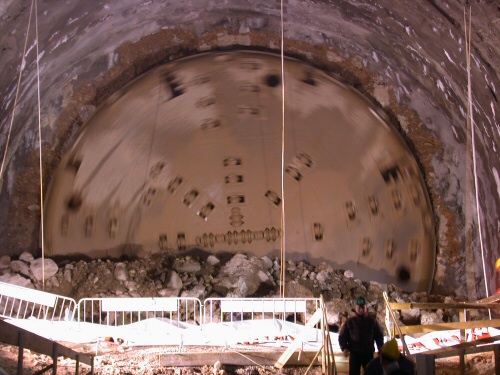
Il contesto operativo in uno scavo con TBM scudata è radicalmente diverso da quello che si trova in uno scavo con tecniche tradizionali. Le problematiche sono quelle tipiche di un ambiente produttivo, anche se in ambiente confinato, e si può dire che tale fase è gestita da uno stabilimento mobile che produce galleria staticamente finita. I principali rischi presenti in lavorazioni di questo tipo sono i seguenti: rischi per movimentazione di carichi pesanti (rifornimento, spostamento e montaggio conci, smontaggio/montaggio binari di scorrimento del back-up e sostituzione cutters della testa fresante); investimento (in particolare causato da mezzi per i rifornimenti); caduta dall’alto (in particolare zona erettore, per il montaggio dei conci, e testa, per la manutenzione); rischi derivanti da contatto con parti in movimento (in particolare nella zona di prolungamento nastro in coda al back-up); elettrocuzione; incendio. Oltre a questi vi sono quelli normalmente presenti in un contesto di tipo industriale (officina, uso di paranchi, manutenzioni elettriche e meccaniche) e quelli ambientali, di cui si dirà più avanti.
Nelle lavorazioni potenzialmente più pericolose, come la movimentazione dei conci (con carichi di 17-20 t per la fase di rifornimento e di 8,6 t per l’approvvigionamento della slitta e all’erettore) non si sono registrati incidenti. Nelle operazioni di smontaggio/montaggio binari di scorrimento del back-up si sono verificati 2 infortuni dovuti a disattenzione: una distorsione tibio-tarsica (scivolata durante le operazioni di spostamento) ed una frattura composta ad una falange (martellata su un dito), le conseguenze. Tra le operazioni di routine più delicate c’è sicuramente la sostituzione dei cutters, che comporta rischi nella movimentazione dei pezzi (un singolo cutter pesa 120 kg) e rischi di scivolamento o di caduta dall’alto all’interno della testa fresante. Queste operazioni sono in genere effettuate dal personale più esperto e si è dovuto registrare un solo incidente durante tutto il corso dei lavori, dovuto ad una grave violazione procedurale. Nell’operazione di smontaggio è previsto l’arretramento della testa dal fronte e, successivamente, lo sblocco del cutter, che viene appoggiato su un’apposita slitta da cui viene rimosso per mezzo di un paranco. In occasione dell’incidente il caposquadra ha proceduto alla rimozione dei fissaggi del cutter senza arretrare la testa dal fronte e, per effetto della pressione sul fronte di scavo, il pezzo è rimasto incastrato nella sua sede. A questo punto, invece di procedere al riposizionamento dei fissaggi, è stata movimentata la testa per sbloccare il cutter, il quale è saltato dalla sua sede e, dopo un rimbalzo, ha colpito di striscio al piede lo stesso responsabile delle operazioni. Il tutto si è risolto con un serio trauma da schiacciamento, anche se le conseguenze avrebbero potuto essere di ben altra portata.
Nelle altre operazioni con rischio di caduta dall’alto, in particolare sull’erettore durante l’imbullonamento dei conci, non si sono registrati infortuni anche per l’imposizione dell’obbligo di uso di DPI anticaduta come dispositivo di sicurezza supplementare nei punti più elevati ed esposti. Si è invece avuto un grave incidente in circostanze anomale ed imprevedibili, fortunatamente senza conseguenze permanenti, per una caduta dal ponte superiore del back-up. Due lavoratori asportavano una griglia di pavimentazione nei pressi della vasca di decantazione delle acque, per calare i fanghi alla piattaforma sottostante, peraltro interdicendo l’area con nastro bianco e rosso a debita distanza. Un altro lavoratore scavalcava i nastri e, mentre andava a prendere un badile, precipitava dall’apertura procurandosi un trauma cranico con frattura della mandibola e della mascella e contusioni multiple. Le conseguenze, decisamente favorevoli per una caduta di quasi 6 metri, permettevano al lavoratore di rientrare regolarmente al lavoro dopo 70 giorni.
Anche il rischio di investimento, particolarmente rilevante negli scavi in tradizionale e qui strettamente correlato alla fase dei rifornimenti, è stato sostanzialmente eliminato imponendo, compensandola come onere di sicurezza specifico, l’adozione di una piattaforma girevole per l’inversione degli automezzi pesanti che ha evitato prolungate e pericolose retromarce. L’unico investimento registrato in galleria è stato causato da un furgone che durante una manovra ha urtato un lavoratore, procurandogli però solo contusioni leggere.
Per eliminare i rischi derivanti da contatto con parti in movimento, il nastro trasportatore è stato interamente schermato. Nella zona di coda, dove si installano le prolunghe del supporto nastro, è stata imposta la schermatura mobile dei nastri, rimovibile solo a nastro fermo durante le operazioni di giunzione della prolunga del supporto. Sono state fatte eseguire anche delle prove specifiche di tenuta del manicotto di iniezione del pea-gravel, al fine di eliminare il rischio di sfilamento della tubazione in pressione. Per evitare problemi dovuti ad errato posizionamento del manicotto, il tubo è stato sempre assicurato con cavi di sicurezza. Sia nelle fasi di prolungamento nastro che di iniezione non si sono registrati problemi.
La gestione dell’impianto elettrico (prolunga alimentazione e manutenzione) è stata affidata a personale specializzato e si è svolta regolarmente. Per il rischio incendio la macchina è stata dotata di estintori a polvere ed a CO2 a distanze ravvicinate e di un’attrezzatura completa per la squadra degli addetti all’emergenza. Il piano di evacuazione è stato predisposto e verificato con la collaborazione dei Vigili del Fuoco di Trento. I punti più importanti della TBM sono stati costantemente sorvegliati dall’impianto a circuito chiuso in cabina di regia ed è stato sempre presente un collegamento telefonico di rete fissa a bordo. I monitor di controllo della macchina sono poi stati costantemente replicati nell’ufficio della direzione di cantiere, tramite una linea dati dedicata.
A fronte dei 5 infortuni accaduti nelle attività potenzialmente pericolose (236 giorni di assenza per inabilità temporanea con una media di 47,20 giorni/infortunio), se ne sono registrati 14 nelle normali attività lavorative (295 giorni di assenza per inabilità temporanea con una media di 21,07 giorni/infortunio): 9 per scivolate o cadute camminando (5 nei normali passaggi pedonali della TBM e 4 sui conci); 2 per scivolate alla base dello scudo, durante operazioni di manutenzione; 2 durante operazioni sui conci; 1 per la caduta di una scheggia di calcestruzzo. Le conseguenze più rilevanti si sono avute per le cadute accidentali (3 distorsioni tibio-tarsiche, 1 frattura composta del polso e, in generale, contusioni), mentre per gli altri infortuni si sono avute solo lievi contusioni.
Complessivamente nel ciclo scavo - rivestimento delle due gallerie si sono verificati 19 infortuni, di cui 1 grave (senza conseguenze permanenti), per totali 531 giorni di assenza per inabilità temporanea con una media di 27,95 giorni/infortunio. Anche in questa fase il fattore umano (disattenzione o non elevata professionalità) è stato determinante nella dinamica degli incidenti occorsi.
Dovendo giudicare la sicurezza intrinseca di una TBM, ancora si deve scindere la macchina in due parti distinte: lo scudo-testa fresante, dove si concentra la tecnologia di una TBM, è quella più curata ed intrinsecamente sicura; il back-up, che può pure essere prodotto da terze parti, è quella più ordinaria e, dal punto di vista della sicurezza, la parte più delicata, suscettibile com’è di continue variazioni nel corso di uno scavo.
Nella parte anteriore della TBM sono state rilevate delle lacune nelle protezioni dell’erettore, che sono state modificate, integrando le procedure delle lavorazioni relative. Il back-up ha invece richiesto diverse modifiche, soprattutto riguardo alle protezioni per il rischio di caduta dall’alto, ed ha comportato, soprattutto nella prima fase di utilizzo, un lungo lavoro di messa a punto.
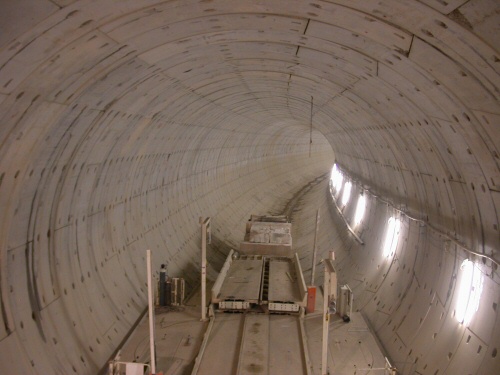
- polveri (valore limite 10 mg/mc): 0,80 mg/mc;
- anidride solforosa (limite 5,2 mg/mc): 0,07 mg/mc;
- ossido di azoto (limite 31 mg/mc): 0,09 mg/mc;
- monossido di carbonio (limite 29 mg/mc): 0,001 mg/mc;
E’ stata pure effettuata la misurazione del gas radon (isotopo Radon-222), utilizzando dei campionatori passivi che hanno fornito valori pari a 9 Bq/mc, mediati in un arco di tempo di 3 settimane. Il valore è risultato inferiore ai livelli fissati per i luoghi di lavoro sotterranei (livello di esposizione 500 Bq/mc - media annuale).
Il documento di valutazione dell’esposizione dei lavoratori al rumore, ai sensi del D.Lgs. 277/91, ha evidenziato che quasi tutti i lavoratori impiegati nella TBM avevano un livello di esposizione personale giornaliera LepD > 90 dBA (valore massimo 96,7 dBA). I lavoratori impiegati in fresa sono stati quindi formati ed informati sugli obblighi e sui rischi in relazione al rischio rumore.
E’ stata pure eseguita un’indagine fonometrica indipendente per valutare la rumorosità in varie zone della fresa. Si sono rilevati i seguenti valori nelle due fasi del ciclo di avanzamento (fase 1: montaggio anello - fase 2: scavo):
- zona a ridosso della testa (fasi 1 - 2): 85,9 dBA - 125,8 dBA;
- passaggio testa-1° carro (fasi 1 - 2): 93,9 dBA - 116,9 dBA;
- zona centrale motori (fasi 1 - 2): 93,8 dBA - 103,3 dBA;
- zona posteriore motori (fasi 1 - 2): 100,1 dBA - 118,4 dBA;
- zona trasporto conci (fasi 1 - 2): 91,6 dBA - 115,5 dBA;
- slitta (fase 1): 103,0 dBA;
- sala regia (fase 2): 81,7 dBA;
- coda macchina (fase 2): 86,4 dBA.
Il problema dell’esposizione dei lavoratori alle vibrazioni non è stato studiato nel dettaglio, dal momento che la normativa specifica (D.Lgs. 187/2005, recante prescrizioni minime di sicurezza e di salute relative all’esposizione dei lavoratori ai rischi derivanti da vibrazioni meccaniche) è entrata in vigore dal 1 gennaio 2006, a scavo pressoché ultimato. In futuro questo aspetto di sicurezza e di salute del lavoro non potrà più essere trascurato, poiché durante lo scavo con TBM la trasmissione di vibrazioni non è trascurabile.
(pubblicato su Scienza & Mestieri N. 1/2006 - Trimestrale del Collegio degli Ingegneri del Trentino)
[torna su]